Josef Ganter Feinmechanik supports its customers in all phases of a given project. Alongside CNC-mining, our service portfolio also includes upstream and downstream processes, such as development and construction, blasting, sliding surface grinding, polishing, component assembly, engraving, inscription, labelling or regulatory affairs management. Further technical processing options, such as wire eroding, electropolishing, varnishing and others, can be offered with our partner companies within the Klingel medical metal group or with external suppliers as a system solution.
Design to manufacture
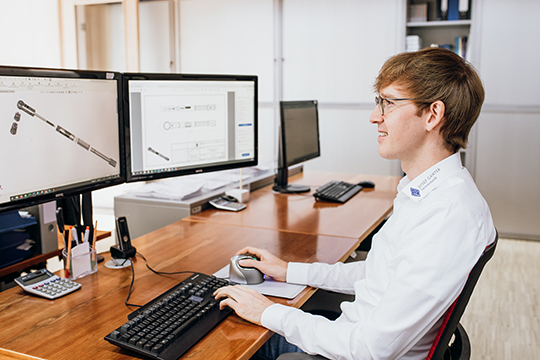
Efficient processes thanks to optimised design.
Optimal design with the lowest possible costs: in medical technology as well as in all areas where metal precision is a fundamental requirement, product and process solutions must be planned and implemented in as efficient and sustainable a manner as possible. With our experienced engineering teams with the greatest proximity to the production process, we offer our customers well-founded advice for perfected production and process solutions when it comes to design and costs.
CNC machining
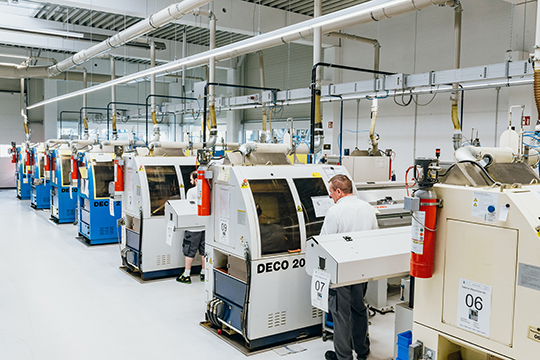
We turn with ease.
The art of precise turning: Josef Ganter Feinmechanik has a modern machine fleet operated by experienced cutting machine mechanics. Small and large series as well as customer-specific sample parts are produced on over 30 CNC long-turning lathes and turning and milling centres with up to ten axes. Here, a diameter range of 0.5 mm to 32 mm is covered. All the machines are equipped with fully automatic bar loaders of the manufacturers FMB and LNS. We can thus produce very high production quantities extremely economically. Our CNC turning lathes are equipped with rear processing and motorised tools. Thus, complex long-turned parts with a wide variety of milling, drilling and impacting operations can be manufactured on a drawing-conforming basis. By using B-, C- and Y-axes, we are able to manufacture even the most complicated turned parts without further post-processing.
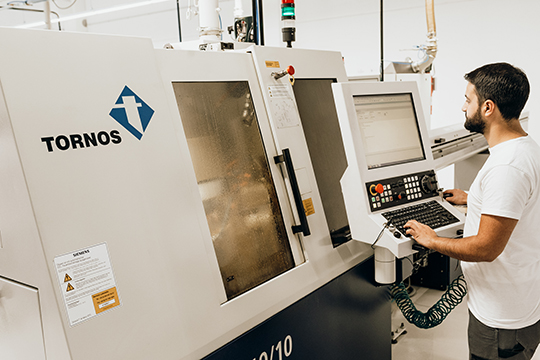
High-tech for high-end products.
We process our microparts on Swiss-type turning machines with which the smallest dimensions and the narrowest tolerances can be achieved, as the references from the traditional clock industry, for instance - a trademark of Swiss precision - show to this day.
Surface treatment
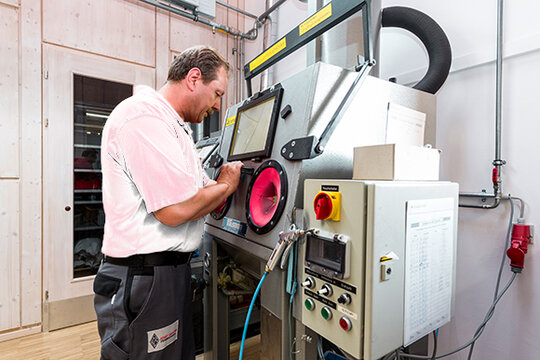
We make surfaces shine.
We blast, for example, with glass pearls and corundum in order to process the outerlying surfaces and to produce homogeneous, matt-shining end contours.
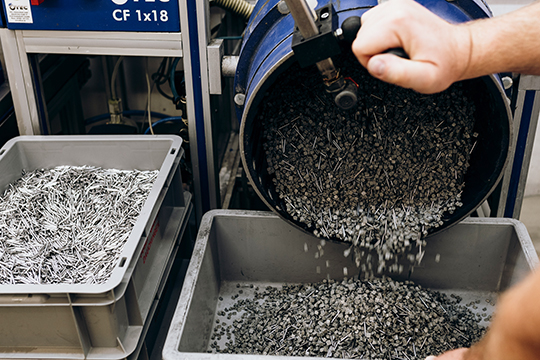
For the perfect finish.
Our vibratory finishing department has a modern disc centrifugal system for the wet and dry grinding of metal parts. In the drum container, these gently receive the perfect finish.<br/>
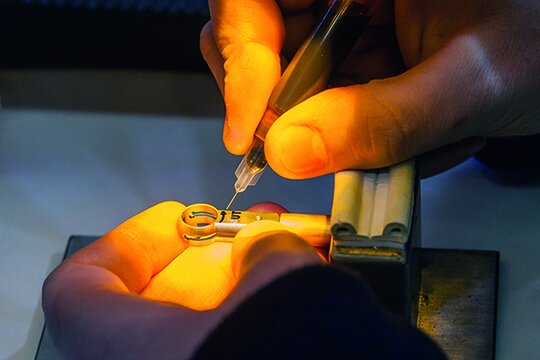
Individual labelling.
Logos, labels, serial numbers, barcode or data matrix code. We label using laser inscription or CNC milling. We label with sterilisable ceramic paint, with monocolour and multi-colour versions possible.
Cleaning
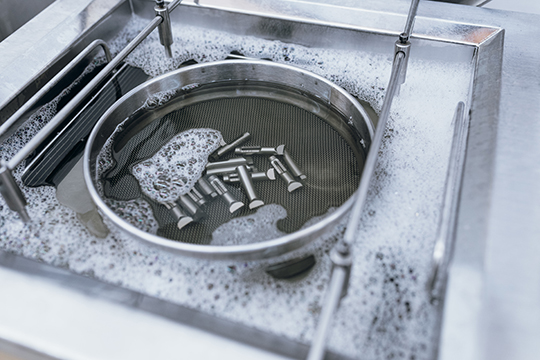
Not just visually clean...
Cleanness and safety are a must for medical technology; for us, therefore, they are a matter of course. This is a central component of our thinking and actions, which makes Josef Ganter Feinmechanik a sought-after production partner for the medical industry. Regulated and standard-based residual dirt requirements regarding the technical cleanness of the products are part of our standard and are demonstrably fulfilled by means of our validated cleaning process. Narrow particle limits from the pharmaceutical sector, demonstrability of micro-organisms below permitted limits and the toxic purity of the products are adhered to and routinely re-evaluated. Here, our qualified 2-tank cleaning system with modified alcohol guarantees us reproducible cleaning results, through which we demonstrably not just fulfil the requirements regarding technical product cleanness, but exceed them.
Assembly/testing
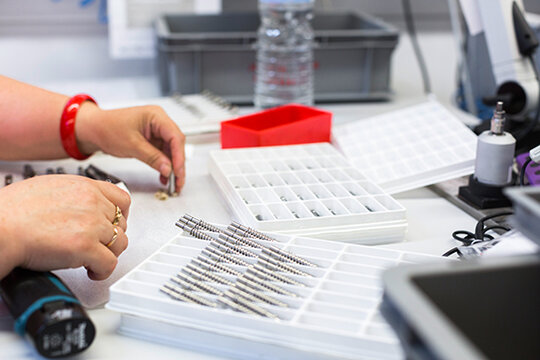
We merge your parts into modules.
The Josef Ganter assembly team specialises in the assembly of even the smallest components. This is seen, for example, in the case of our dental ratchets.
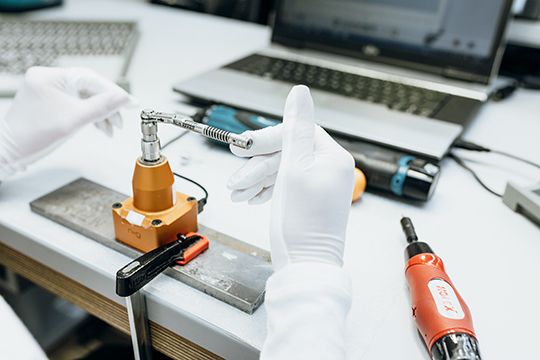
Testing, one two three...
Complex measurements and tests according to standard specifications ensure reliable quality controls, carried out by our qualified specialist personnel. The excellently equipped test centres and measurement rooms are directly assigned to the various production areas. Our own measuring tool monitoring ensures additional safety.
Regulatory affairs
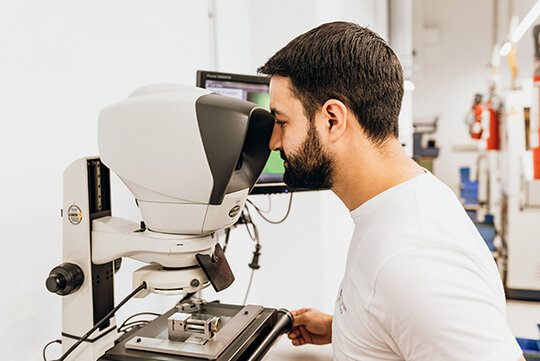
We support you in carrying out your MDR conformity tests.
To support your design responsibility, we provide you with valuable input on creating and maintaining your technical documentation.
As we are an elementary component of the product realisation, we are committed to documenting our process responsibility as a producer.
Packaging
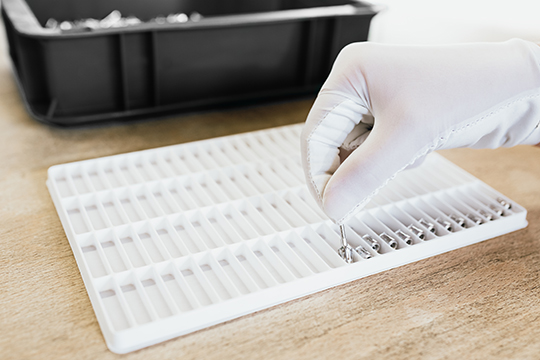
Space-saving and transport-secure.
After final end control, we pack your parts carefully, securely and in a manner that saves space in specially produced and designed packaging.